Introduction: Meaning of Perpetual Inventory Management
Perpetual Inventory refers to the money invested in the form of raw materials such as cotton, wool, plastic, cement, iron, chemicals, etc., for a short period of time. It represents various forms of stock, including raw materials, semi-finished goods, finished goods, indirect materials, and internal parts, which will eventually be converted into money.
Perpetual Inventory is a crucial component of a company’s current assets, alongside payables and cash. According to the Reserve Bank of India (RBI), inventory accounts for approximately 55-60% of current assets. This proportion is even higher in industries like rubber, plantations, and trading, where inventory makes up more than 75% of current assets.
Effective inventory management is essential for businesses to maintain a smooth production process, reduce wastage, and optimize cash flow. One such effective method is the Perpetual Inventory System, which ensures real-time stock monitoring and control.

Perpetual Inventory System: A Smart Approach to Inventory Management
What is a Perpetual Inventory System?
The Perpetual Inventory System is a method of continuously tracking inventory rather than waiting until the end of the year to calculate stock levels. As the name suggests, inventory is updated daily or at fixed time intervals based on purchases and consumption.
For example:
- A company starts with ₹10 lakhs worth of inventory.
- The next day, it purchases ₹4 lakhs worth of inventory, bringing the total to ₹14 lakhs.
- If ₹5 lakhs worth of inventory is used in production, the stock reduces to ₹9 lakhs.
- Later, another ₹3 lakhs of inventory is purchased, increasing stock to ₹12 lakhs.
- After using ₹5 lakhs of inventory for production, the balance becomes ₹7 lakhs.
This process continues, ensuring that inventory records always reflect the current stock.
Implementation of Perpetual Inventory System
A continuous inventory system requires detailed record-keeping of goods received and consumed. This is achieved through:
- Bin Cards – A manual record of stock movements.
- Goods Ledger – An accounting record showing stock levels.
The balances in the bin card and goods ledger must always match the actual inventory. If discrepancies arise, a thorough investigation is conducted.
Advantages of the Perpetual Inventory System
- Real-Time Stock Updates
- Businesses can check stock levels anytime and compare them with book records.
- Simplifies Control & Monitoring
- Continuous tracking makes it easier to detect stock discrepancies and take corrective actions.
- Prevents Over-Stocking & Stockouts
- Ensures that raw materials are available as needed, preventing production delays.
- Reduces Year-End Calculation Hassles
- Eliminates the tedious task of manually calculating stock at the end of the year.
- Improves Employee Accountability
- Employees responsible for inventory management are monitored effectively.
- Ensures Smooth Production Flow
- By maintaining proper inventory levels, the production process remains non-stop and uninterrupted.
Cost Disadvantages of holding inventory
Just as there are two sides to a coin, there are two sides to keeping inventory. On the one hand, the advantages of keeping inventory are obvious
happens On the other hand, there are costs-disadvantages of keeping inventory. The cost-disadvantages of inventory holding can be listed as follows:
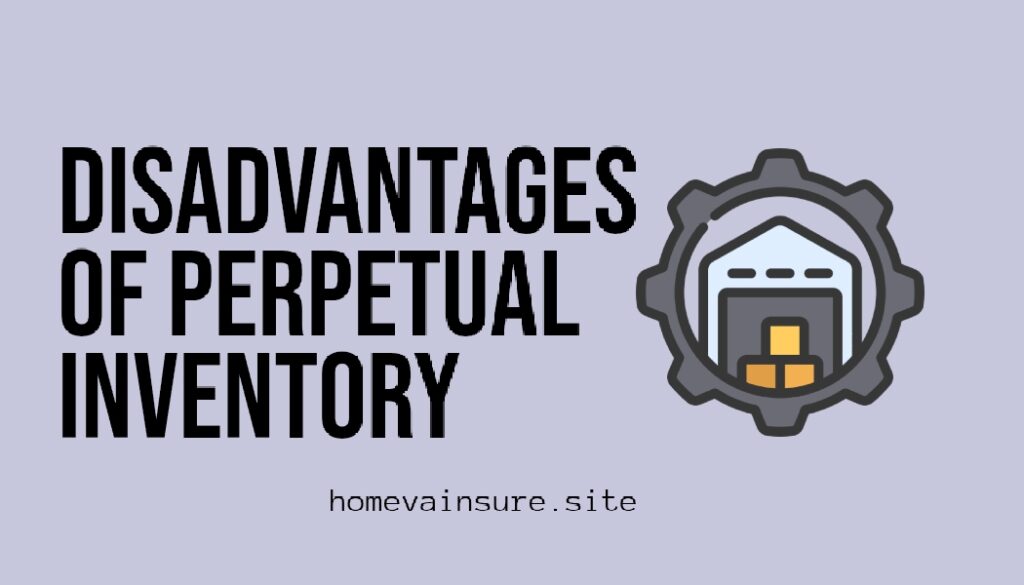
Perpetual Inventory
Carrying cost :
- The cost incurred in maintaining the inventory can be called carrying cost, it increases. Interest is incurred on the working capital invested in maintaining inventory because if that capital was not invested in inventory, it could have been invested elsewhere and earned interest or profitably used to earn a return, this is also called an alternative cost or alternative arrears.
Liquidity risk :
- Liquidity risk is to the extent that money invested in inventory cannot be converted into cash quickly.
Carrying cost :
- As the inventory increases its carrying cost – the cost of handling the goods also increases. Also, insurance premiums, rent, burglary-fire, accident risk, etc. are included in the maintenance cost, which adds up.
Spoilage-Incident Cost :
- Spoilage in holding inventory for too long-
- Increases the chance of falling. Loss of quality due to leakage of liquid, escape of air, dropping of other goods, spoilage increases.
Cost of obsolescence :
- Cost of obsolescence is higher as inventory becomes obsolete due to scientific research and changing fashion.
Depreciation Losses :
- Depreciation losses are caused by keeping inventory longer. It has to be endured. Sometimes the tax burden also increases.
Cost of placing order :
- Repeated ordering of goods doubles the cost. Like filling of order form, dispatch, postage cost, correspondence cost, stationery cost, verification cost, accounting cost, clerical cost etc. doubles. Instead, reducing the number of orders and placing a larger order can prevent the recurrence of such expenses.
An important function of inventory management is to determine and maintain the optimum level of inventory, balancing the benefits and losses, by comparing the benefits of holding inventory with the costs of holding it.
Example Calculation of Perpetual Inventory
A factory maintains the following records for raw material “A”:
- Average consumption: 100 units per week
- Minimum consumption: 50 units per week
- Maximum consumption: 150 units per week
- Uniform quantity: 600 units
- Lead time: 4 to 6 weeks
Find:
- Uniform Surface (Maximum Stock Level) Uniform Surface=Maximum Consumption×Maximum Lead Time\text{Uniform Surface} = \text{Maximum Consumption} \times \text{Maximum Lead Time}Uniform Surface=Maximum Consumption×Maximum Lead Time =150×6=900 units= 150 \times 6 = 900 \text{ units}=150×6=900 units
- Minimum Stock Level Minimum Stock=Minimum Consumption×Minimum Lead Time\text{Minimum Stock} = \text{Minimum Consumption} \times \text{Minimum Lead Time}Minimum Stock=Minimum Consumption×Minimum Lead Time =50×4=200 units= 50 \times 4 = 200 \text{ units}=50×4=200 units
- Reorder Level Reorder Level=Maximum Consumption×Lead Time\text{Reorder Level} = \text{Maximum Consumption} \times \text{Lead Time}Reorder Level=Maximum Consumption×Lead Time =150×4=600 units= 150 \times 4 = 600 \text{ units}=150×4=600 units
These calculations help maintain a balanced inventory and prevent stock shortages.
What is Perpetual Inventory Management?
Perpetual inventory refers to the money invested in raw materials, semi-finished goods, finished goods, and internal parts that will eventually be converted into cash. It helps businesses track stock in real-time.
Why is inventory an important part of current assets?
Inventory, along with cash and payables, forms a major part of a company’s current assets. According to RBI, it accounts for 55-60% of current assets, and in some industries, it can be over 75%.
What is a Perpetual Inventory System?
It is a system where inventory is updated continuously instead of being calculated at the end of the year. Stock is recorded in real-time as purchases and usage happen.
How does a Perpetual Inventory System work?
Example:
A company starts with ₹10 lakhs worth of inventory.
Buys ₹4 lakhs worth of stock → Total = ₹14 lakhs
Uses ₹5 lakhs for production → Stock reduces to ₹9 lakhs
Buys ₹3 lakhs more → Total = ₹12 lakhs
Uses ₹5 lakhs → Stock = ₹7 lakhs
This process continues to ensure accurate stock tracking.
What are the tools used in a Perpetual Inventory System?
Bin Cards – Manual record of stock movements.
Goods Ledger – Accounting record of stock levels.
What are the advantages of a Perpetual Inventory System?
Real-time stock updates
Prevents overstocking & stockouts
Reduces year-end stock calculation effort
Improves employee accountability
Ensures smooth production flow
What are the cost disadvantages of holding inventory?
Carrying Cost – Storage, insurance, and maintenance expenses.
Liquidity Risk – Inventory takes time to convert into cash.
Spoilage Cost – Risk of damage, leakage, or loss of quality.
Obsolescence Cost – Outdated stock due to new trends.
Depreciation Losses – Reduction in inventory value over time.
Order Placement Cost – Repeated ordering increases paperwork and admin costs.
How are inventory levels calculated?
Maximum Stock Level = Maximum Consumption × Maximum Lead Time
= 150 × 6 = 900 units
Minimum Stock Level = Minimum Consumption × Minimum Lead Time
= 50 × 4 = 200 units
Reorder Level = Maximum Consumption × Lead Time
= 150 × 4 = 600 units